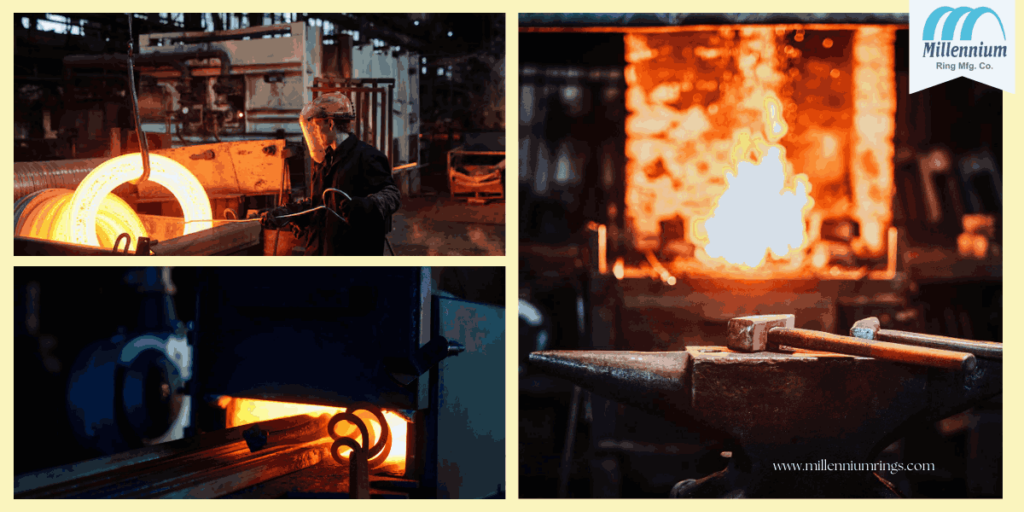
Table of Contents
ToggleIntroduction
For centuries, the forging industry has formed the basis of manufacturing, and moldings metals into robust components for different use cases. Smart manufacturing has transformed traditional forging in recent years, enhancing efficiency, precision, and sustainability.
Innovations like automation, AI (artificial intelligence), and IoT (Internet of Things) are turning the closed-die and open-die forging methods smarter in smart manufacturing.
In this blog, we have discussed the automation of forged parts and how smart manufacturing is empowering forging processes, especially Closed-Die Forging Ring, Forging Ring, Seamless Rolled Rings, and Rolled Ring Forgings.
Closed-Die Forging vs. Open-Die Forging
Metalworking process in which metal is shaped using localized compressive forces. The main two forging method types are closed-die and open-die forging:
- Closed-Die Forging: This solution, otherwise known as impression-die forging, utilizes dies that have predetermined cavities intended to shape the metal as desired. The optimal process for creating high-strength, complex components such as Closed-Die Forging Rings.
- Open-Die Forging: The workpiece is simply deformed between flat or simple dies which do not completely enclose the workpiece. Larger components that need high durability are often created using open-die forging.
Read More: Closed Die Forging vs. Open Die Forging
Smart Manufacturing in Forging — what is it?
Intelligent Manufacturing: Manufacturing refers to the process of transforming conventional industrial processes by incorporating digital technologies to develop streamlined production models that reduce waste and improve the quality of the final product. In forging, smart manufacturing does mean:
- Automation and Robotics: Speeding up and standardizing production
- Filters and Sensor Data Fusion: Enabling anticipation of process issues.
- AI and ML: Optimum forging and predictive maintenance.
- Data Analysis: Improving decision-making and minimizing material waste
- Digital Twins: Building virtual models to simulate and optimize forging.
How Does Smart Manufacturing Solve Their Challenges In Closed Die Forging?
Several methods such as smart manufacturing have enhanced closed-die forging by improving precision and reducing wastage of material. Here’s how:
- Machine Learning for Quality Assurance: When using AI, the Forging Ring can pass the Feather Test.
- Predictive Maintenance: Detecting wear of the equipment and preventing downtime.
The Ultimate Guide to Robotics in Automated Material Handling
Process Optimization: Digital twins simulate forge conditions to optimize processes prior to physical production.
This ensures we have well-engineered Closed-Die Forging Rings that are stronger, and reliability consistent.
Bringing Intelligence to Open-Die Forging through Smart Manufacturing
Smart manufacturing technologies also contribute to open-die forging in numerous ways:
- Real-Time Monitoring: IoT sensors provide real-time data to modify force, temperature, and other parameters.
- AI-Enabled Refinements: Machine learning algorithms calculate ideal forging routes.
- Sustainability Factors: The energy consumption can be minimized through an optimized heat cycle.
- Improved Safety: Automated systems eliminate human exposure to dangerous environments.
These technologies ensure uniformity and durability, essential for large-scale production of Seamless Rolled Rings and Rolled Ring Forgings.
How Does the Forging Industry Benefit from Smart Manufacturing?
Smart manufacturing aspects in forging provide multiple advantages:
- Increase of Efficiency: Automation not only streamlines production but also improves quality.
- Enhanced Quality Control: AI-based inspections identify defects early on.
- Less Waste: Machining to precision lessens wasted material.
- Cost Reductions: Energy-saving reinforces operational cost optimization.
- Improved Customization: Flexible and adaptable manufacturing through digital technologies.
All these advantages provide highly ideal conditions for Forging Rings with high quality.
Challenges in Realizing Smart Manufacturing in Forging
Although it has its benefits, introducing smart manufacturing to the forging industry brings challenges:
Switching to smart systems involves a lot of investments and capital.
- Technical Know-How: Advanced machinery needs skilled workers to operate this equipment.
- Cybersecurity Threats: More connected means more vulnerable.
- Interoperability: They may not have compatibility with the new technologies.
Overcoming these challenges is essential for a smooth transition to smart forging processes.
Trends in Smart Manufacturing for Forging
Here are a few upcoming trends in smart manufacturing for the forging sector.
- Integration of Artificial Intelligence: AI will be used as an input in the further Integration of AI
- Advanced Robotics: The robots will work alongside humans (cobots).
- Sustainable Practices: Sustainable practices will be implemented.
- 5G Connectivity: Faster Data Transmission for Real-Time Process Adjustments
- Supply Chain Transparency with Blockchain: Traceability of materials
Our developments along with Seamless Rolled Rings and other forged components will further enhance these processes.
Overall Future of Forging in Smart Manufacturing
Real-time monitoring, AI-driven optimization, and automation are well employed for all the processes of Closed-Die Forging Rings and Open-Die Forging.
Though there are challenges, ongoing technological advances will make forging processes even more efficient, cost-effective, and environmentally friendly. The forging future is more innovative, quality-focused, and globally competitive in the direction of smart manufacturing with the support of industries.