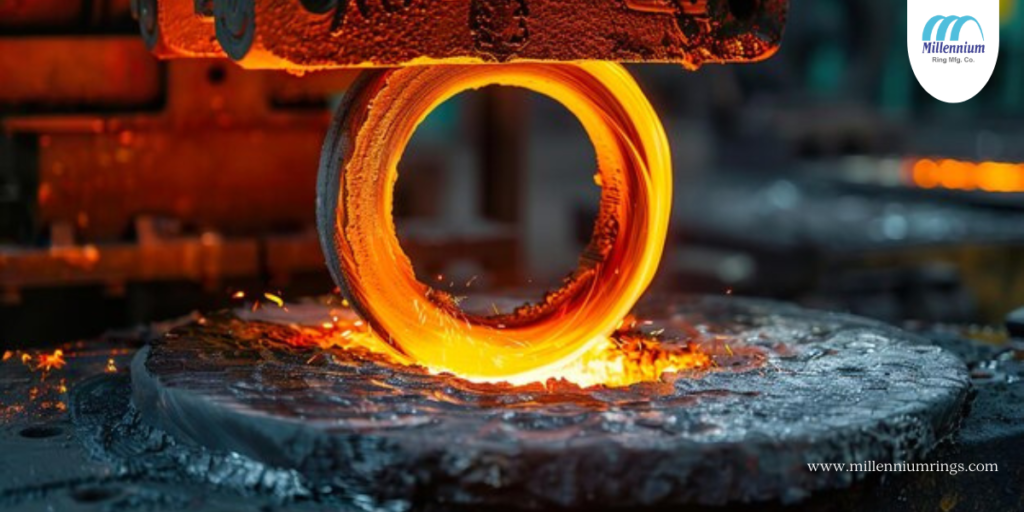
Table of Contents
ToggleIntroduction: Exploring the Various Forging Processes in Metal Technology
Forging is one of the most popular metalworking methods. This method is useful and common among manufacturers. It is useful to produce some metal structures that are impossible for human hands and machines to carve with perfection.
If a manufacturer is keen to produce complex shapes, picking the right Forging Process is the key. With each step, the manufacturer can produce components with precise tolerance and complex details. The produced equipment is widely known among industries like automotive, aerospace, and energy.
Also, forging processes are efficient in different terms. These methods are useful for mass production of components at lower cost. This is why it is widely popular. In this blog, you will understand how these forging methods work based on the requirements of users.
Understanding Metal Forging: Key Processes and Techniques
Forging is the method that brings life to the metals. Products prepared through this method are strong and carry the best mechanical properties.
The forging method is one of the primitive and most popular metalworking procedures.
Metal Forging Process can give the materials the desirable hardness and toughness. This is how the applications of such metals are huge among industrial usages.
Each forging method carries significance for manufacturers, such as:
- Provide better grain structure.
- Perfect for mass production
- Bring durability and exceptional strength to the manufactured components.
- Unleash higher mechanical properties of metal
- Produce more reliable products.
However, several methods are associated to produce various types of components. They are useful in different circumstances. So, each process is useful something unique and special designs.
1. Open-Die Forging: Flexibility for Large and Complex Shapes
As said earlier, forging methods are many to follow. However, special equipment can only be forged by following the ideal processes. When it comes to go with Open Die Forging, it is the one that gives a free shape to the metal.
The use of large compressive forces is common. In the process, free-flowing material movement is useful. Also, there is no specific mold used in this forging method. That’s why it is ideal to produce complex shapes and equipment.
Applications of this forging method are common in heavy industry:
- Shafts, rudder posts, and structural parts.
- Drill bits, pressure vessels, and wellhead equipment.
- Crane shafts, gear blanks, and couplings.
- Excavator arms, bulldozer blades, and construction booms.
- Large axles, wheels, and rail components in the railway industry.
- Large gears, shafts, and other critical components for mining equipment.
The materials applicable in the Open Die Forging method are aluminium, titanium, steel, etc.
When it comes to the open-die forging, they are as follows:
- Useful for elongating the metal.
- Better to manage a metal’s thickness.
- Achieve greater strength and durability of equipment.
- Offer great flexibility for large components.
2. Closed-Die Forging: Precision for High-Volume Production
The heated metal is useful to forge in many forging methods. It is known as Closed-Die Forging. In this forging method, there is a pre-shaped mold. The operator uses machines to provide tremendous pressure to fill the mould cavity.
Products manufactured in this process are tough and fine. They exhibit higher tolerance and display the art of fine details.
The closed mould ensures the dimensional shape of every produced piece. The products are manufactured in the method of closed-die forging:
- Turbine blades, structural components, and landing gear parts.
- Engine parts like connecting rods, crankshafts, and camshafts.
- Hand tools like wrenches, hammers, and pliers.
- Industrial tools like dies, punches, and clamping devices.
- Energy sector components like turbines, compressors, and valves.
- Medical industry tools like surgical tools, orthopaedic implants, and prosthetics.
The advantages of using Closed Die Forging are also interesting. They are:
- Useful to produce less amount of waste
- Valid for completing complex shapes
- Appropriate for expensive metal forging.
- Great to provide mass production.
- Marvellous precision to get in the results.
- Maintain higher consistency.
3. Ring Rolling: Strengthening Circular Components for Demanding Applications
When it comes to picking a Forging Process, ring rolling is a popular choice. This method is useful to produce seamless and circular components. There is a pre-formed ring that expands through rolling between two dies.
Durability and resistant products are easy to produce in this forging method. In high-stress conditions, rolled-ring parts perform perfectly. Ring sizes are easier to decide.
The advantages of using the ring-rolling forge method are as follows:
- Allows for the manufacturing of rings in a wide range and various sizes.
- Boosts grain structure.
- Provide maximum durability to the products.
The applications of ring-rolling forged products are common in the following industries:
- Aerospace industry.
- Automotive industry.
- Wind power energy.
- Oil and gas industry.
- Power generation unit.
4. Upset Forging: Enhancing Strength with Minimal Waste
In the modern methods of forging, Upset Forging stands tall as well. It is the method that enhances the strength of components. It starts by compressing the material followed by a specific axis.
Unlike Closed Die Forging, upset forging is also responsible for producing strong and durable products. It is responsible for compressing metal along its axis.
This is how it provides the desired shape to the entire metal. Using upset forging, the following equipment is manufactured:
- Crankshafts, axle components, and steering mechanisms.
- Aircraft landing gears, engine parts, and structural components.
- Heavy-duty fasteners, bolts, and rods.
- Drill bits, pipelines, and wellhead equipment.
The application of the products produced under upset forging are applicable in the following industries:
- Automotive industry
- Aerospace
- Construction and infrastructure
- Oil and gas industry.
Conclusion
Any type of forging process you choose is invaluable. It plays an important role in creating high-performance and durable metal components. The method is responsible for improving the mechanical properties of metal. This is why it becomes superior to casting or machining. Many industries that require equipment with strength, reliability, and precision, rely heavily on forged parts.
With the advancement of forging machines and techniques, it continues to offer enhanced tremendous results day by day. By understanding these key processes, businesses can select the best approach for their needs. Forging remains essential for ensuring the highest quality and performance in metalworking.