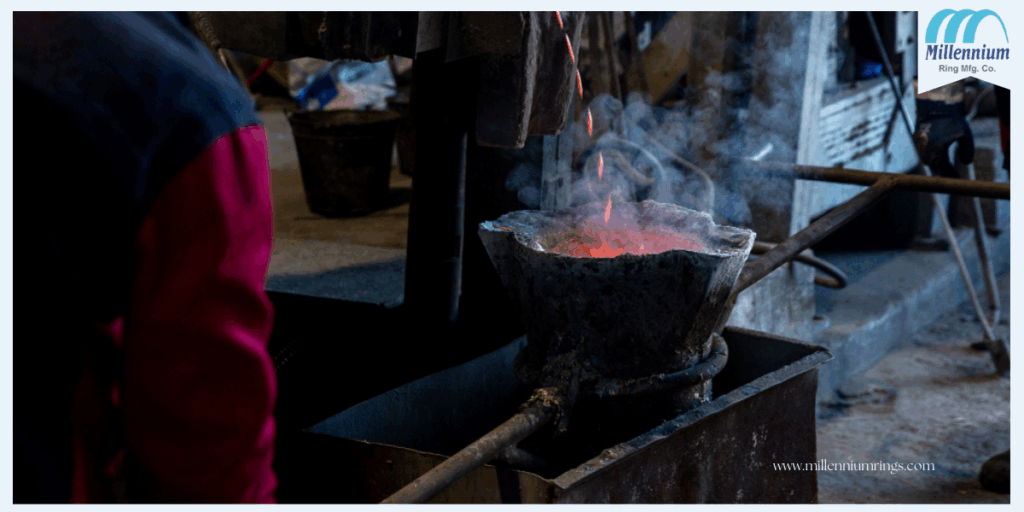
In high-performance sectors such as aerospace, automotive, and heavy machinery, the strength, precision, and reliability of components cannot be compromised. Closed Die Forging process is a unique manufacturing process that is best suited there. Closed Die Forging is important in modern industries, allowing the manufacture of precise, durable, and custom-formed metal components.
On this page, we detail the process, its main benefits, and why it’s well-suited for difficult parts such as forged rolled rings and custom-forged components.
Table of Contents
ToggleAn Introduction to Closed Die Forging
Impression-die forging, also known as closed-die forging, is a manufacturing process that makes use of dies which take the shape of the pre-cut profile of the part. As the dies are brought together, the metal is squished into the cavity under high pressure until its shape matches that of the cavity.
This method is usually done with heated billets of steel, aluminum, or alloys. The billet is formed precisely, forcing out excess material (flash) as it is compressed within the die. That results in a near-net-shape part with little need for machining.
Closed Die Forging Process consists of:
- Die plotting and prep (typically CNC-machined for precision)
- Heat the billet to make it more ductile
- Pressured die closure and material flow
- Trimming of flash
- Heat treatment for high mechanical properties
- Final inspection and optional finishing
Read More: The Role of Smart Manufacturing in Closed-Die and Open-Die Forging
Importance of Precision in Complex Components
Inconsistencies are not something that high-performance parts industries can afford. This is particularly important when it comes to Custom Forged Components like turbine blades, engine components, or even transmission gears. These components have to withstand high loads, temperature variations, and dynamic stress.
Precision in geometry dictates:
- Proper fitment and assembly
- Optimized stress distribution
- Homogeneous material properties over the component
- Lowered post-processing (milling, grinding, etc.)
Because closed die forging is highly repeatable and capable of producing highly detailed components, it is superior to cast or open-die forging for complex designs.
The Biggest Benefits of Closed Die Forging
The benefits of closed die forging are much more than all-around accuracy.
Here are some of the main reasons it is used for critical components:
A. Improved Mechanical Properties
The grains are refined and align with the geometry of the part, which gives forged parts greater strength. This results in:
- Higher tensile strength
- Greater impact resistance
- Improved fatigue performance
B. Better Surface Finish and Accuracy
Machining of closed-die forgings is not usually required. These combine to minimize material waste and manufacturing time.
C. High Production Efficiency
After the dies are made, parts can be quickly forged for a medium- to high-volume production run, often with repeatable quality.
D. Material Optimization
In comparison with open-die forging or machining from billet stock, better utilization of raw material is driven by flash control and material flow efficiency.
E. Design Flexibility
This allows complex geometries such as thin sections, undercuts, or complex profiles to be achieved, allowing for innovations in the shape of the part.
What Types of Applications are Closed Die Forged?
Closed-die forging process is essential in industries where reliability and performance are requirements.
Here are a few examples:
A. Aerospace and Aviation
Forged components are used for their strength-to-weight ratio and fatigue resistance in aircraft engine parts, landing gear components, and control systems.
B. Automotive & Transportation
Closed die forged parts encompass everything from gears to steering knuckles and are critical to safety and durability in cars.
C. Power Generation
Wind turbine components, such as forged rolled rings, must meet high strength and thermal requirements to withstand the operating environment and related challenges.
D. Oil & Gas
Drilling and extraction happen in extremely harsh conditions, and demand for tough parts such as valves, flanges, and connectors, many of which are closed-die forged.
E. Construction and Mining Machinery
Whatever the application, heavy-duty equipment such as bulldozers and excavators requires durable and reliable (forged) components.
How does Millennium Rings Produce High Precision Closed Die Forgings?
Millennium Rings is a leading manufacturer of closed die forgings, which are manufactured to conform to the most exacting industrial standards. We produce various types of custom forged components using our latest forging technology and experienced craftsmanship.
- High-performance Forged Rolled Rings for energy and power segments
- Components for aerospace and defense
- Machine and automation systems geometries.
Our Process Advantage:
- Precision tooling with advanced CAD/CAM die design
- Real-time inspection and testing in Integrated Quality Control
- From prototype to high-volume orders, Flex Production
- Heat treatment and machining capabilities in-house for turnkey solutions
What differentiates us is that we are completely focused on customization and working with our customers. Collaborating with engineers & project managers to develop cost-effective forging solutions while maximizing performance for quick implementations.
Conclusion
Closed Die Forging: The Best Way To Manufacture Complex Parts. The choice of Custom-Forged Components for industries that cannot afford any change in performance is due to its capacity to generate parts of consistent quality while significantly reducing material wastage.
The closed die process represents a strong and efficient path forward, whether high volume production or one-off, precise parts, such as forged rolled rings, are the main goal.
Followed by readers such as Millennium Rings, innovators in the industry, businesses are assured to receive forged solutions designed to last in the harshest of environments.