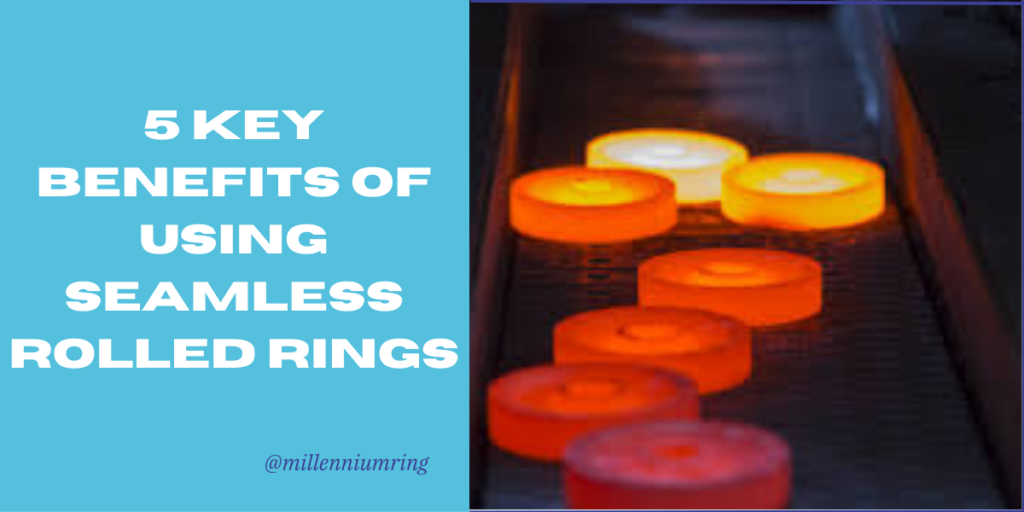
Table of Contents
ToggleIntroduction
Seamless rolled rings hold a vital part in different industrial applications. It offers a scope of benefits that add to the effectiveness and unwavering quality of machinery and equipment. The accuracy-designed parts are produced using advanced techniques. It helps make them a fundamental piece of industries like aviation, oil and gas, and automotive, from there, the sky is the limit.
In this article, we will investigate the five key benefits of using Seamless Rolled Ring in industrial applications.
1.Superior Strength and Durability
One of the essential benefits of seamless rolled rings lies in their uncommon strength and toughness. These parts are fashioned from a single piece of material. It wipes out the need for welding or different joints that could compromise structural integrity. The Rolled Ring Forging system adjusts the grain construction of the metal. It upgrades its general strength and protection from exhaustion and effect. After that, seamless rolled rings are mainly used under heavy loads and harsh conditions. It makes them ideal for basic applications where being reliable is the principal.
- High-pressure vessels and reactors: High-pressure vessels and reactors are critical in chemical processing, oil and gas, and power age industries. They need seamless rolled rings for parts like flanges, closures, and heads. The rings ensure regulation and safety under huge tension.
- Bearings and gears: Bearings and gears benefit from rolling contact. They benefit from the wear-resistant and layered strength of seamless rolled rings. This strength leads to longer help life and fewer maintenance needs.
- Heavy machinery components: Heavy machinery components depend on seamless rolled rings. Cranes, development equipment, and other large machines use them for basic parts like shafts, pins, and bushings. Rings add to the machines’ strength and life span.
2.Cost-Efficiency and Material Savings
Seamless Ring Rolling offer a practical answer for industrial applications. This is because of their one-of-a-kind assembling process. The forging strategy limits material waste, as is the exact forming of the ring. It guarantees the ideal utilization of raw materials. This is not at all like customary assembling strategies that include machining from a bigger bar. It doesn’t project, the forging process to boost the usage of material. It adds to the cost reserved funds and environment sustainability. Also, the strength of seamless rolled rings reduces the need for replacement. This also lowers long-term support costs.
- Reduced material waste: It is nonstop and limits waste. This contrasts with conventional methods. It saves money and cuts environmental harm.
- Lower energy consumption: Rolling regularly requires less energy than forging, adding to a more economical assembling process.
- Expanded life expectancy: The prevalent strength and durability of seamless rolled rings mean longer part life, decreasing replacement frequency and added costs.
3.Customizable Design and Flexibility
Seamless Rolled Rings give an elevated degree of plan flexibility. It permits the manufacturers to modify the aspects, shapes, and materials as per t industrial requirements. The Ring Forging system empowers the improvement of seamless rings through complex geometrics and design profiles. As such, it meets the assorted necessities of various applications. This aspect guarantees that seamless rolled rings can be custom-made to fit an extensive variety of hardware and gear. It further helps in upgrading their similarity and implementation across different ventures.
The rolling system refines the grain structure, prompting further developed properties like:
- Upgraded ductility and formability: Certain metals rolled using specific strategies have improved pliability. This allows for complex shapes and intricate designs to be formed without reducing strength.
- Superior surface finish: Rolling makes a smooth, reliable surface. It reduces internal pressure and makes the metal more resistant to weakness.
- Tailored properties: By choosing explicit composites and rolling cycles, manufacturers can accomplish properties. These are erosion opposition, high-temperature implementation, or non-magnetic behavior.
4.Superior Dimensional Precision
The controlled, constant rolling cycle guarantees exceptional dimensional accuracy and consistency in seamless rolled rings. This means a few advantages:
- Decreased machining necessities: The tight resilience accomplished through rolling limit the requirement for broad machining, saving time and cost while bringing down material waste.
- Improved assembly and performance: Exact aspects empower immaculate components and planning. It prompts smoother activity, diminished vibration, and upgraded general implementation.
Compatibility: With reliable aspects across clusters, seamless rolled rings offer unrivalled compatibility, improving upkeep and fixing Ring Rolling Process.
Read More: The Process of Seamless Rolled Ring
This accuracy makes them ideal for applications like:
- Hydraulic cylinders and pistons: Hydraulic cylinders and pistons have tight resiliences. These keep activity release-free and smooth. This is key for precise control in hydraulic systems.
- Aerospace components: Aerospace components must be very precise. The needs of the aeronautic trade demand it. Seamless rolled rings succeed around here, adding to the unwavering quality and safety of basic airplane parts.
- Scientific instruments and tooling: Scientific instruments and tooling rely on high-accuracy seamless rolled rings. The rings are key in instruments needing precision and repeatability. These include optical gear, measuring devices, and jigs.
5.Consistent Material Properties
Uniform material properties are critical for guaranteeing the solid presentation of industrial parts. Seamless rolled rings are known for their steady material properties all throughout the whole design. Not at all like castings as it might show varieties of material thickness and properties. So, seamless rings fashioned from a single piece of material proposition a serious level of consistency. This consistency adds to solid implementation, settling on seamless rolled rings. It became a favored choice for basic applications where accuracy and consistency are fundamental.
The rolling system refines the grain structure, prompting improved properties like:
- Enhanced ductility and formability: Certain metals rolled utilizing explicit strategies show improved flexibility. It takes into consideration the complex shapes and unpredictable design plans.
- Superior surface finish: Rolling creates a smooth, steady surface. It reduces internal pressure and improves exhaustion resistance.
Custom fitted properties: Producers can achieve custom properties by choosing specific combinations and rolling cycles. They can get properties like corrosion resistance, high-temperature performance, or non-magnetic behavior.
This flexibility makes seamless rolled rings reasonable for different applications like:
- Corrosion-resistant component: Synthetic and marine conditions request materials that can endure brutal circumstances.
- High-temperature applications: Seamless rolled rings produced using heat-safe alloys track down use.
- Specialized applications: Seamless rolled rings have special properties. They enable use in applications with unique material needs.
Conclusion
All in all, the use of seamless rolled rings in industrial applications gives a scope of advantages. It includes strength, durability, cost-productivity, flexible plan, proven uprightness, and steady material properties.
These benefits make seamless rolled rings an imperative part of different ventures. Here reliability quality, implementation, and effectiveness are essential. Technology keeps rising. The need for design components, like seamless rolled rings, grows. This solidifies their significance in the industry.