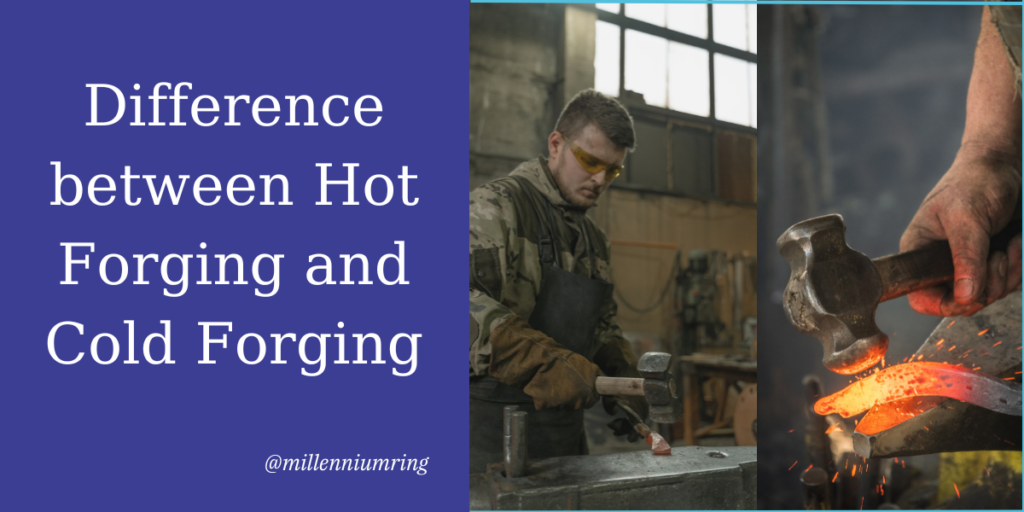
In the world of metalworking, forging stands out as a fundamental process for shaping metals into desired forms. Two primary methods, hot forging, and cold forging, each offer unique advantages and are employed based on specific applications.
In this comprehensive guide, we’ll explore the distinctions between hot forging and cold forging, shedding light on their processes, advantages, applications, and the factors that differentiate them.
Table of Contents
ToggleHot Forging vs. Cold Forging: An Overview
Aspect | Hot Forging | Cold Forging |
Temperature | High temperatures (above recrystallization) | Room temperatures or slightly elevated |
Material Hardening | Minimal | Significant |
Tolerance Precision | Moderate to low | High |
Production Speed | Slower | Faster |
Tool Wear | Higher | Lower |
Material Suitability | Ferrous and non-ferrous metals | Limited to certain materials |
Costs | Typically higher | Often more cost-effective |
Hot Forging Process
Hot forging is a metalworking process that involves shaping metal at elevated temperatures, typically above its re-crystallization temperature. This temperature range enhances the material’s plasticity, making it more malleable and easier to deform. The hot forging process is widely used to manufacture a variety of components across different industries due to its ability to produce parts with improved mechanical properties and reduced internal stresses.
The Hot Forging Process Typically Includes the Following Key Steps
Material Selection: The process begins with the careful selection of the appropriate material based on the desired properties of the final component. Commonly used metals for hot forging include steel, aluminum, titanium, and various alloys.
Heating: The chosen metal is heated to a temperature above its recrystallization point, which is specific to the material being forged. This high temperature allows the metal to become more ductile and less resistant to deformation.
Deformation: Once the metal reaches the desired temperature, it is subjected to deformation using mechanical forces. This can be achieved through processes like hammering, pressing, or rolling, depending on the complexity and size of the component being forged.
Die Design and Tooling: Dies and tooling play a crucial role in shaping the metal into the desired form. The design of the dies is customized based on the specific geometry and dimensions of the final component.
Cooling: After the metal is formed, it undergoes controlled cooling to prevent rapid cooling and minimize the risk of internal stresses. This controlled cooling process helps enhance the mechanical properties of the forged part.
Trimming and Finishing: The forged component may undergo additional processes such as trimming, machining, or other finishing operations to achieve the required tolerances and surface quality.
Advantages of Hot Forging
Improved Form ability: Hot forging allows for the shaping of complex and intricate components that might be challenging to achieve through cold forging or other manufacturing processes.
Enhanced Mechanical Properties: The elevated temperatures during hot forging prevent the material from working hardening, resulting in components with improved mechanical properties such as ductility and toughness.
Wide Range of Materials: Hot forging can be applied to a broad range of materials, including both ferrous and non-ferrous metals, providing versatility in manufacturing.
Reduced Energy Consumption: In certain cases, hot forging can be more energy-efficient compared to cold forging because less force is required to deform the material at elevated temperatures.
Minimized Material Waste: Reduced material waste is another advantage of hot forging, contributing to a more sustainable and cost-effective manufacturing process.
The hot forging process is chosen when a combination of enhanced formability, improved mechanical properties, and versatility in material selection is required for the production of durable and reliable metal components.
Applications:
Commonly used for larger components and those requiring minimal precision, hot forging is suitable for materials like steel, aluminum, and titanium.
Cold Forging Process
Cold forging is a metalworking process that involves shaping metal at or near room temperature. Unlike hot forging, which takes place at elevated temperatures, cold forging occurs with the metal in a solid state. This process is widely utilized to manufacture precision components with intricate shapes and tight tolerances. Cold forging is known for its efficiency, minimal material waste, and ability to produce high-quality parts for various applications.
The Cold Forging Process Typically Includes the Following Key Steps
Material Selection: The process begins with the careful selection of the material. Cold forging is commonly used for metals such as aluminum, copper, brass, and certain alloys that exhibit good ductility at room temperature.
Billet Preparation: The selected metal is cut into a specific shape, known as a billet, to facilitate the forging process. The billet is often pre-heated slightly to improve its formability.
Die Design: Dies play a critical role in shaping the metal into the desired form. The die design is customized based on the complexity and dimensions of the final component. Cold forging often involves multi-station dies to achieve intricate shapes in a single operation.
Forging Process: The billet is placed in the die cavity, and the forging process begins. Cold forging operations include processes such as extrusion, coining, and upsetting. These processes deform the metal without heating it significantly.
Trimming and Finishing: After the initial forging, the component may undergo additional processes such as trimming, machining, or other finishing operations to achieve the required tolerances and surface quality.
Advantages of Cold Forging:
High Precision and Tight Tolerances: Cold forging is known for its ability to achieve high precision and tight tolerances, making it suitable for applications where accuracy is crucial.
Improved Surface Finish: The cold forging process often results in a smoother surface finish compared to hot forging, reducing the need for additional machining.
Material Savings: Cold forging generates less material waste compared to some other manufacturing processes, contributing to cost savings and sustainability.
Increased Strength: Cold forging can result in increased material strength due to work hardening, especially in certain alloys.
Faster Production Speed: Cold forging is generally faster than hot forging
Applications:
Ideal for small to medium-sized parts requiring high precision, cold forging is commonly used for materials like aluminum, copper, and certain alloys.
Frequently Asked Questions (FAQ)
Q1: What are the primary advantages of hot forging?
A: Hot forging offers advantages such as improved formability, reduced energy consumption, and the ability to forge a wide range of materials, including both ferrous and non-ferrous metals.
Q2: Why choose cold forging over hot forging for certain applications?
A: Cold forging is preferred when precise tolerances, excellent surface finish, and minimal material waste are crucial. It’s often more cost-effective for smaller and more intricate components.
Q3: How does temperature affect the material properties in hot forging?
A: The elevated temperatures in hot forging prevent the material from working hardening, resulting in components with minimal internal stress and improved ductility.
Q4: Are there limitations to the size of components that can be cold forged?
A: Cold forging is more suitable for smaller to medium-sized components due to the limitations posed by the lower forces applied at room temperatures.
Q5: Which method is more environmentally friendly?
A: Cold forging is generally considered more environmentally friendly as it requires less energy and produces less material waste compared to hot forging.
Conclusion
In the world of metal forging, understanding the differences between hot forging and cold forging is crucial for selecting the right method for specific applications. While hot forging offers advantages in terms of formability and versatility, cold forging excels in precision, efficiency, and material conservation.
By weighing the unique characteristics of each process, manufacturers can make informed decisions, optimizing their production processes to meet the demands of diverse applications in various industries.